The metal fabrication process is multi-faceted, and its applications are equally broad. Here we give a brief overview of what to expect from the procedure.
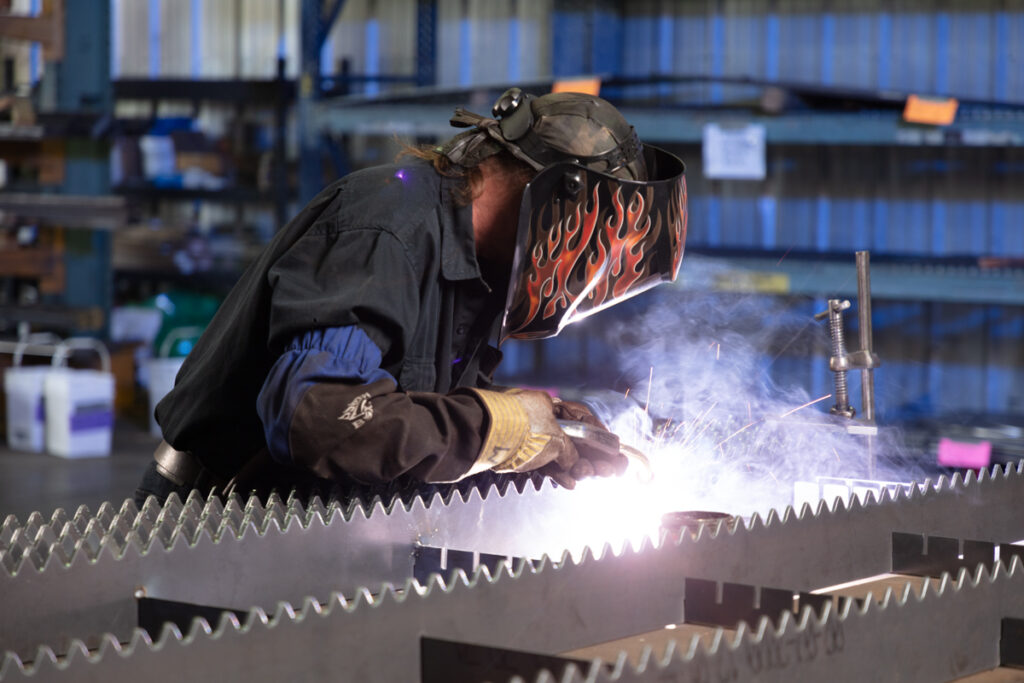
What Is Metal Fabrication?
Metal fabrication is the process of taking raw metal and transforming it into a finished product. It is a fundamental component of nearly every industry on the planet, commercial, industrial, and structural. Whether you are looking at massive steel structural beams or small screws in your Ikea table, these are the results of metal fabrication.
While many people reduce the metal fabrication process into welding alone, welding is only a small part of the fabrication process. In truth, it often also includes cutting, assembling, machining, burning, and assembling metal components into the final product a manufacturer wants to sell you, and at every stage of the process, there are experienced professionals making the work happen.
What Are the Steps for the Metal Fabrication Process?
Metal fabrication requires many different steps to craft the metal into the specified product. These vary slightly depending on the industry and certainly for the customer, but the following are the most common steps in the process.
Designing
The first step of metal fabrication is to design the finished product. This is generally done with CAD (computer aided design) software. In such programs, drawings can be rendered precisely to the measurements required, accounting for complete accuracy despite inherent complexity. CAD also allows engineers and designers to test the models for performance. In this way, a 3D prototype of an object can be created before any metal is cut or shaped. Once the designs are complete, they can usually feed directly into welding machines for cuts that meet specifications precisely.
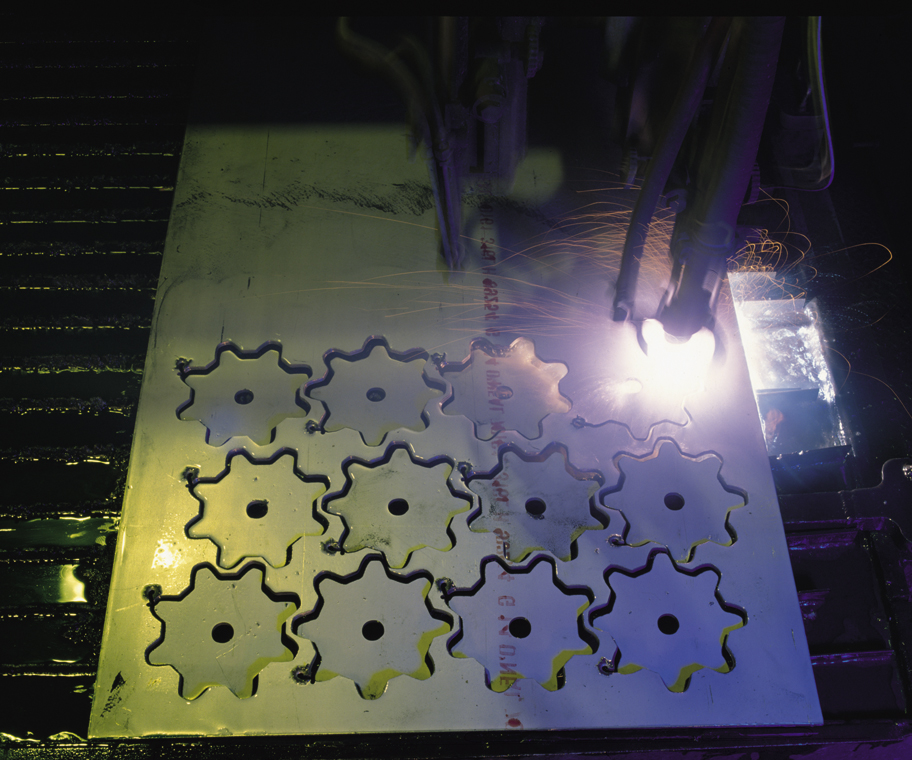
Fabrication
Fabrication itself describes the process of shaping metal as intended. This includes cutting, bending, and assembling. Usually the metal in question is plate metal which is typically at least two inches thick.
Cutting
Cutting plate and sheet metal requires a great deal of force concentrated into fine precision. To master this dichotomy, there are several ways to accomplish the cutting part of the metal fabrication process. The best one for the project depends heavily on the kind of metal being cut, its thickness and hardness, and how precise the cuts need to be.
Laser cutting, water jet cutting, and mechanical shearing are three kinds of metal cutting that have low tolerance for error. They may require tools such as lathes, mills, shears, and nibblers. Again, these tools follow the specifications enumerated within the computer blueprints to make sure they are precisely what the client is looking for.
The most precise way to cut sheet metal is to utilize a laser or other high-energy incision. At Norfolk Iron & Metal, it is common for us to use plasma cutting, especially when we need to make intricate designs or work with extreme accuracy.
Other Reductive Methods
Cutting is not the only reductive process involved in metal fabrication. Here are some other common techniques:
- Punching—Like using a hole punch on paper, punching utilizes a hardened metal punch (and a die underneath) to punch through metal plate. It is an effective way to remove excess material from the work surface.
- Shearing—The shearing process uses sharp blades almost like scissors to slice straight lines through metal, especially flat sheet metal like steel, aluminum, or brass.
- Blanking—Best applied to softer metals in sheets or strips, blanking punches out metal pieces with a die. The pieces punched out with blanking are typically larger than that produced by punching.
- Notching—Notching is an excellent method for creating cuts and angles that are too detailed for the shearing process. It works best with lower volumes and sheet or rolled metals.
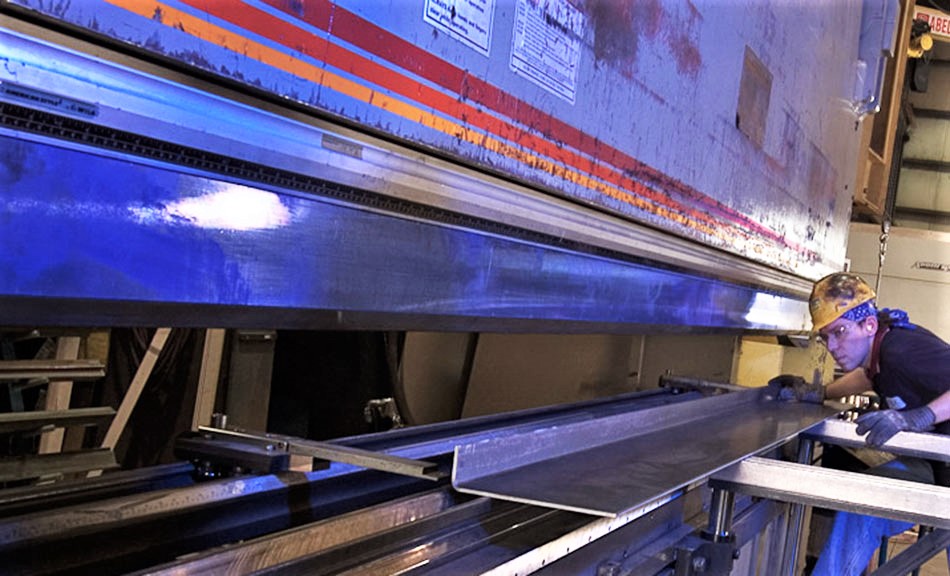
Forming
Forming may be the most nuanced part of the metal fabrication process. Generally speaking, it involves shaping metal to meet the shapes specified in the blueprints, but this is done in so many ways we cannot list them all. The most rudimentary is casting, which involves pouring molten metal into a die or mold and letting it solidify in the required shape. Die-casting adds pressure to the procedure. Casting is ideal for mass production of identical products. Other forming processes include bending, folding, machining, stamping, and punching holes.
Assembling
As the name suggests, assembling involves bringing all of the pieces together to form the final product. Parts need to be fitted together in the correct arrangement, clamped together, and then bonded. How this last is done depends heavily on the design and the application of the piece. Common bonding techniques include riveting, screwing, and (most commonly) welding. The kind of weld employed depends on manufacturer specifications.
Finishing
Finishing is the final touch that makes a product’s fabrication complete. Sometimes it includes painting, rust-proofing, or glazing. Brushing, shining, polishing, and adding decals are all a part of the finishing process. In addition to the aesthetic benefits of finishing, this final step (in conjunction with assembling) strengthens the final product and prepares it for the world.
Installing
Installation is sometimes best handled by the team that created the piece. In this way, they can make on-the-spot corrections or adjustments as needed, lending their skill, expertise, or equipment to the process. Installation services may be applied to anything from large structural elements to more attuned instruments.
Maintaining
Occasionally those who complete the metal fabrication process are also called upon to perform necessary repair or routine servicing. Though this kind of work is less common for engineers and fabrication professionals, it is not uncommon and again ensures that the work is performed with a professional eye.
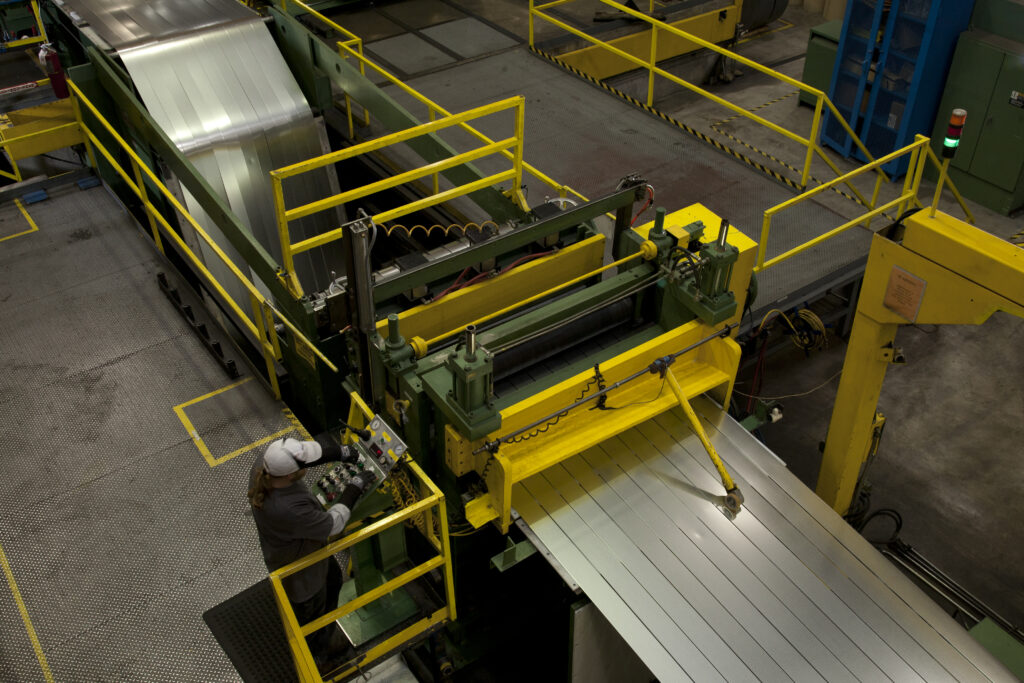
The Future of Metal Fabrication
Metal fabrication is not going anywhere. The process, extensive though it may sometimes seem, is so integral to nearly every industry out there. The metal fabrication process is responsible for creating aircraft parts, both military and commercial; agricultural equipment; automotive and recreational vehicle components; food-processing equipment; construction tools and equipment; communication devices; and energy gathering and processing equipment, just to name a few.
With such broad applications, the metal fabrication process makes for a safe bet career-wise. Any aspect of the process needs people who are interested in the work and willing to see it done well.