If you enjoy working with metal and seeing how it can be shaped into something new, metal fabrication may be a viable career path for you. Warehouse operations specialists spend a lot of their time welding and shaping metal to meet blueprints and other specifications. If that kind of work piques your interest, keep reading to learn more.
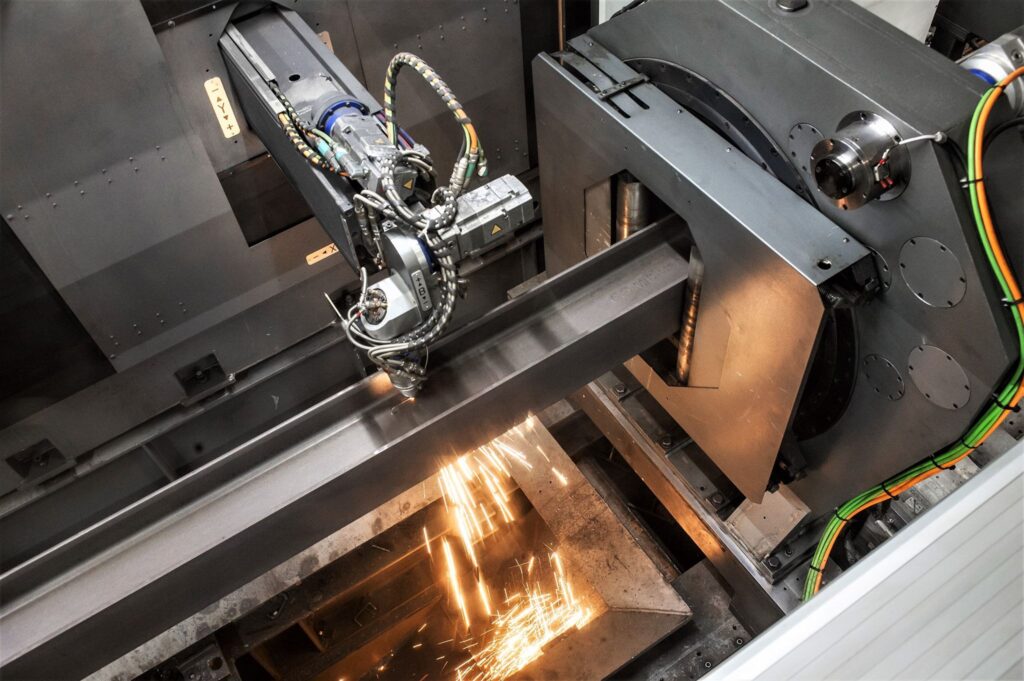
The Job: What Does a Warehouse Operations Specialist Do?
Warehouse operations specialists in commercial or industrial settings are the key personnel in charge of measuring, cutting, positioning, and shaping various kinds of metal. They work in the manufacturing sector in plants and factories, doing work on everything from raw metal to electronic devices, cars, and aircraft, adjusting and assembling according to project specifications.
Accordingly, fabricators must be able to read and understand blueprints, shop drawings, work order booklets, and other plans. With that information, they can make meticulous measurements and cut, notch, fit, and weld materials to the proper specifications. Because tools such as band saws, plasma cutters, flame cutters, shears, ring rollers, drill presses, and press brakes, may be utilized in fabrication, a fabricator must be familiar and competent with each of them. Familiarity with automated equipment and computer-based machinery is also essential.
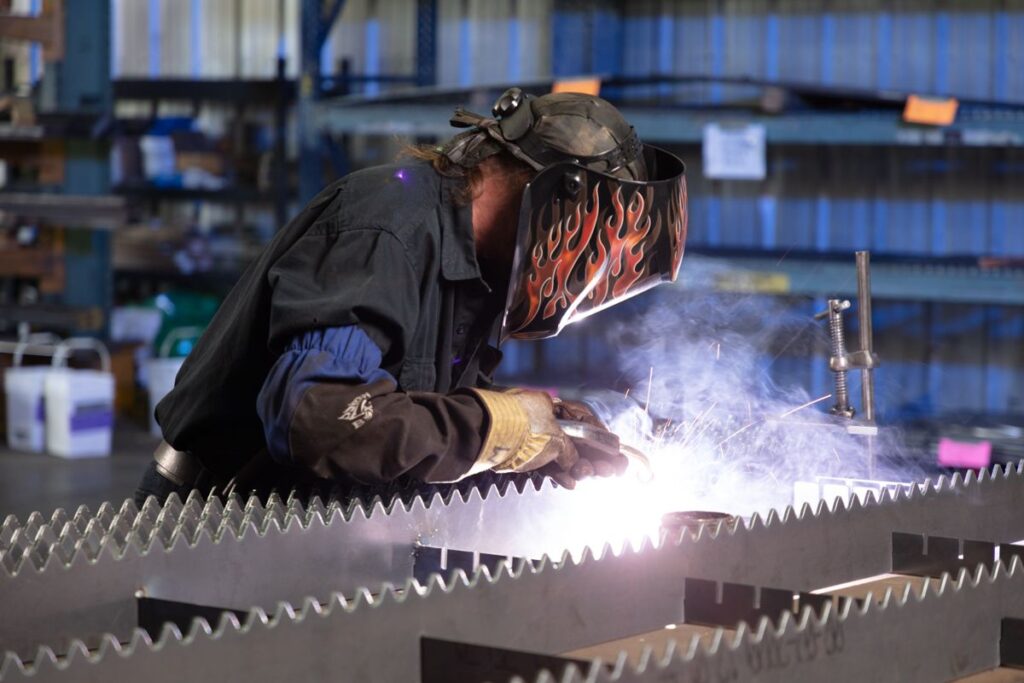
Safety is of the utmost importance. Factory environments are full of hazards, and each employee is responsible for both his or her safety and the safety of those around them. This includes maintaining a clean and organized work area and adhering to all industry standards. All unsafe actions and conditions should be reported to the correct supervisor, and as possible, fabricators should make on-the-spot corrections to improve safety conditions. Wearing proper protective gear, especially eye- and ear protection, is essential.
Warehouse operations specialists may also play a role in finishing metal projects. To achieve proper surface texture they may de-bur and grind metal as necessary. Finished products should be checked meticulously against initial plans. While fabricators may occasionally be asked to perform other work in a project’s timeline, the staple of their workload is the welding process.
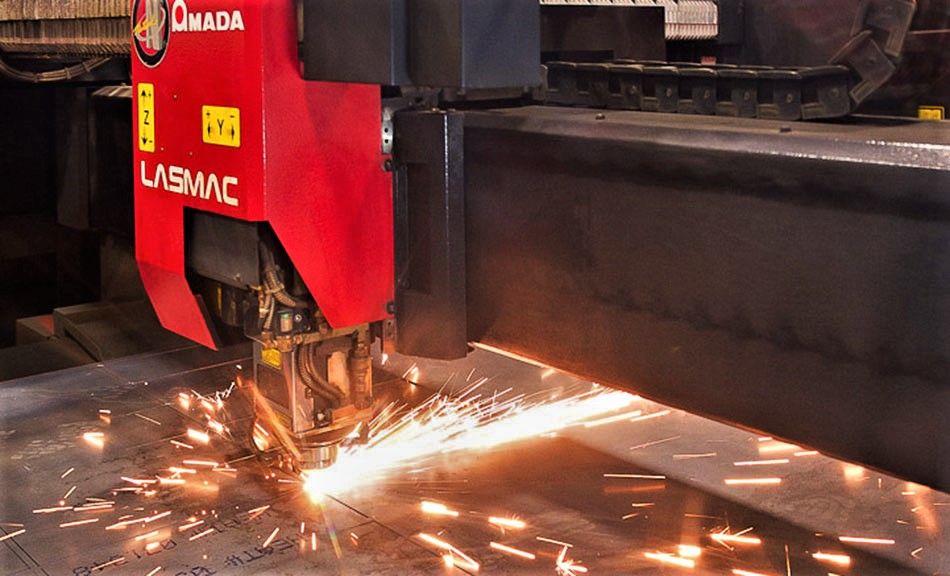
What’s the Difference Between Welding and Metal Fabrication?
Welding is the process of joining metal by applying high heat. It is one of a warehouse operations specialist’s best tools. Fabricators use welding and other metal-shaping methods, including bending and cutting. There are many different kinds of industrial welding, and the most common are MIG and TIG. While both of these methods use an electric arc and a shielding gas, they have some key differences.
MIG Welding
Metal inert gas (MIG) welding—also referred to as gas metal arc welding (GMAW)—uses either a semi- or fully automatic arc to create a weld with a consumable wire which is machine-fed to the weld area and serves as both electrode and the filler material. The shielding gas (usually a mix of 75% argon and 25% CO2) promotes weld penetration, protects the weld, and reduces weld bead porosity.
MIG welding is more effective for joining thick or large pieces of metal. It is faster than its TIG counterpart, reducing production times and, by extension, production costs. The process is relatively easy to learn, but it is less precise than TIG welding. MIG is suitable for a wide variety of applications in welding aluminum and mild and stainless steel that require little to no cleaning and finishing.
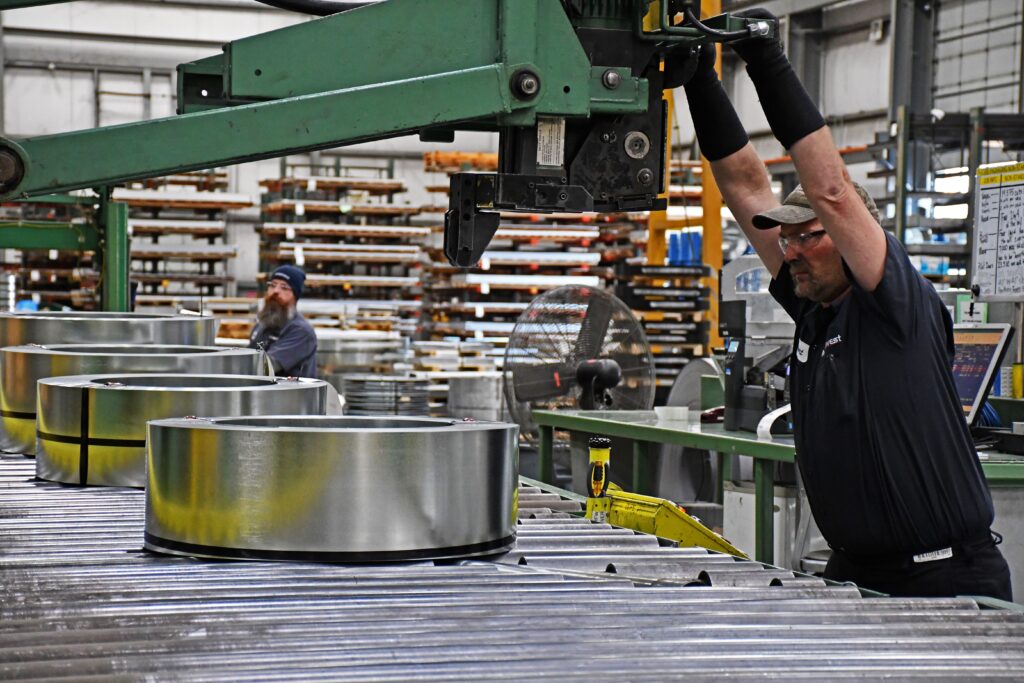
TIG Welding
Tungsten inert gas (TIG) welding is also known as gas tungsten arc welding (GTAW). Like the MIG process, TIG utilizes an arc and shielding gas, but unlike MIG, the electrode used is not consumable. Made of tungsten, the electrode is used alongside a separate consumable filler material, usually a rod which is manually fed into the weld pool. TIG is, therefore, a two-handed process.
Because the process is more involved, TIG welding is more difficult to learn and increases weld times. Precision is this type of welding’s strength and weakness, making it the better choice for working with thinner metals of a wider variety, including copper, aluminum, steel, and titanium. Because TIG is more attuned, it is the first choice of work that requires precision, such as projects in motorsport, industrial construction, and aerospace.